Are Remote Control Aircraft Tugs the Future?
Airplane tugs haven't changed a whole lot over the past few decades. Really, since the inception of diesel tugs over gasoline tugs, they have remained largely unchanged. Sure, they have adopted modern engines, but overall, they are heavy, low-geared tractors to tow airplanes with tow bars.
But times they are a’ changing. There are now a couple of prominent manufacturers of remote control aircraft tugs showing that maneuvering aircraft does not belong to industry monoliths. Indeed, emerging technologies are carving out a niche in even some of the more established industries.
There are two distinct areas in the ground support equipment (GSE) markets that are ripe for technological advances:
- Airplane de-icing, with autonomous units
- Remotely-controlled aircraft tugs
Remote control tugs are already in widespread use across many sectors of the aviation community and even go as far as using automated guided vehicles (AGV) in maintenance and manufacturing.
So, are remote-controlled tugs the wave of the future in aircraft tugs? Let’s find out.
Turn the Aircraft on the Spot
One thing that makes towing with a tug using tow bars is the lack of precise maneuverability. Attaching a tow bar to an airplane's nose wheel adds a pivot point to the turning process. Also, the tug is manipulating the aircraft movement at a position of some 30’-40’ ahead of the nose landing gear, making maneuvering the aircraft much more difficult.
See, the nose gear is designed to make extremely tight turns. Some aircraft can turn the nose gear as far as 90° to the left or the right.
But the same precision levels are impossible with a tug and tow bar. Yes, there are towbarless tugs that offer much more precision than a tug and tow bar combination, but they are still cumbersome and require the same number of ground crew members as a traditional tug.
Remote-controlled tugs do away with this. They offer precision that will never be matched by a traditional tug or even a diesel towbarless tug—remote control tugs load the nose gear directly over the drive wheels, giving them great traction. Also, since they are electric and have no driver on board, they are very low profile; some units are only about a foot in height.
Turning By Moving
Traditional tugs operate under the principle of turning by moving, meaning that the plane must first be moving in a forward direction before the turn can be initiated. So, the tug has to move at least a few feet forward before it can even begin a turn.
On the other hand, remote-controlled tugs have no such requirements. The aircraft is directly on top of the unit, which can perform a zero-point turn. Also, many of these units have a “Lazy Susan” devise, meaning there are no nose gear limitations. The unit itself can take the nose gear well beyond the limits without doing any harm to the aircraft since the nose gear remains stationary.
More Revenue and increased profits with cutting-edge technology
As the old saying goes, you’ve got to spend money to make money.
But is this really true when you’re talking about airplane tugs? Well, let’s take a look at how upgrading to a remote-controlled tug really does pay dividends.
First and foremost, upgrading to one is not financially prudent for every operation. If you aren’t using them all the time (i.e., several times a day) and are only using them occasionally, it may not be worth it to upgrade from traditional aircraft tugs is not necessary, although if you work in crowded hangars even infrequently, a remote control tug is still the perfect solution.
Okay, so let’s think about this: for a standard pushback towing operation attached to the nose wheel, you need up to five personnel:
- Tow team supervisor
- Driver
- Brake rider (for commercial pushback, it’s the pilot, so it doesn’t count against the team)
- 2 ea. Wing walkers
- Tail walker when applicable
Let’s say a team spends two hours per shift towing airplanes. That’s ten man-hours every shift, 3,650 man-hours per year (and the number could be a lot more than this).
A remote-controlled tug can eliminate several of those positions because the operator can move to each position and spot it as it moves.
- No driver
- No wing walkers
- No tail walker
In this same scenario, the smaller team does the same amount of work in 1,460 man-hours, marking a 60% reduction in man-hours over the year. If the airline SOP does not require a brake rider, the whole operation can be done by one person, making it even more efficient.
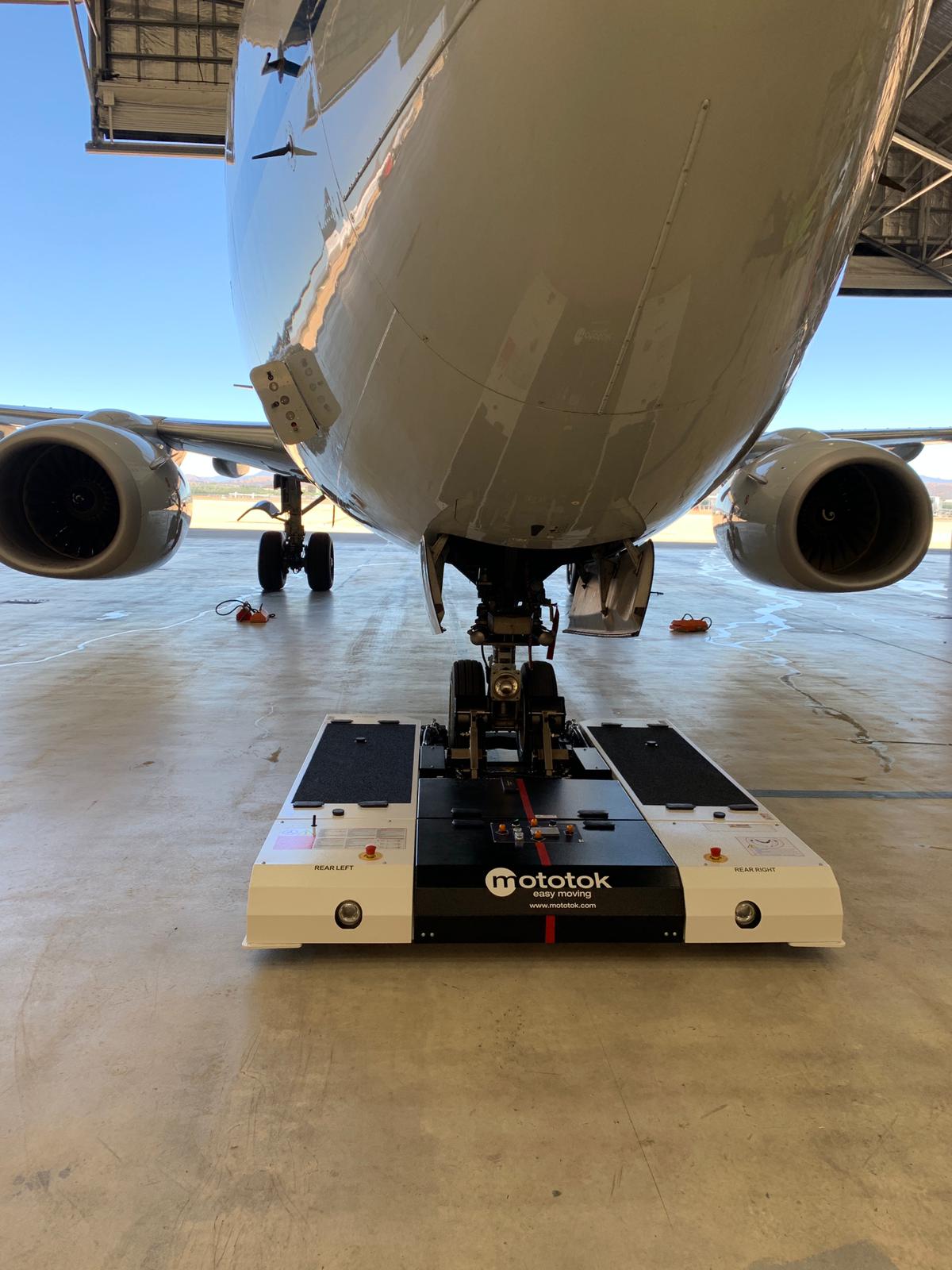
Remote Control Aircraft Tugs Are a Secure Solution
Remote control tugs are also very secure. Unlike reciprocating engines, a battery-powered tug can be fully sealed against the elements, but also for blast protection. But not only are they blast proof, they are some of the only solutions that are safe to use when there are ignitable concentrations of flammable gasses, vapors, and even liquids. Obviously, an internal combustion engine is not a good idea when there are ignitable vapors, but certain electric tugs are rated to work in those environments.
More Revenue = Increased Profits With Cutting-Edge Tech
You’re in business to increase profits. If you are in the government sector, you are in the business of doing a lot more with a lot less. Let’s be real for a few minutes: the military is having the worst recruiting in decades, and the civilian aircraft technician workforce is at a crisis point.
There are simply fewer technicians to go around, whether your operation is public-sector or private-sector. And it takes years to change these trends, so the shortage of techs isn’t going anywhere anytime soon.
The best way to bridge these gaps in personnel is to use technology, especially for tasks that, while extremely important, are also menial. When using technology that simplifies the process, personnel not specifically trained in aircraft ground movements can be cross-trained to perform the task.
In military circles, this means that specialists who generally have more downtime than the APG shop (the shot responsible for aircraft movements) can be easily trained to run a remote control tug, freeing up APG operators to do other things.
Oversteering Protection = Nose Gear Safety
It’s impossible to rank which part of the towing procedure is the most important, but preventing oversteering is definitely up there. Safely turning the nose gear is important to maneuver the tug and note and strictly follow the nose gear limitations.
Thankfully, most remote control tugs are equipped with a turntable that the nose wheels are locked on top of. The table turns, so the nose gear is never turned. In fact, the tug can turn a full 180° and push the jet backward
More Safety Measures, Increased Situational Awareness By Groundcrewmen
Every remote tug on the market has an automatic shut-off, or what some of us know as a “dead man’s switch,” meaning you hit the red button (there are usually a few on the machine and one on the remote), and the unit stops instantly.
Old-school tugs simply do not have the same level of safety. The order to stop has to be relayed from the supervisor to the driver, and they are really loud. It is not uncommon for the driver to miss the instruction, which is a serious risk.
Electric tugs are practically silent, so while there may be other noises on the flightline, at least the loud diesel engine right behind the driver isn’t one of them. Plus, there will only be the operator's reaction time in play rather than their reaction time, time in communication, and then the reaction time of the tug driver.
Greenwood Aerospace Is Your Trusted Partner In GSE
Greenwood Aerospace understands how important high-quality GSE is to your mission. GSE does not get the appreciation it deserves, but we get it. Without reliable GSE, your mission will come to a standstill.
Greenwood Aerospace is committed to cost savings for your operation, no matter the size or location. We work with industry leaders to procure the right GSE for your mission. Or, if you need a steady supply chain of parts for your GSE fleet, Greenwood Aerospace has you covered. Give us a call, and we’ll get started!