The intricacies of aviation logistics are controlled by a network of efficiency and preparedness, where the fine line between mission success and setback is traced to proper inventory management and aircraft sustainment. This is a subtle dance of supply, demand, logistics, and anticipation that ensures the availability of aircraft parts precisely when and where they are needed. In this landscape, aviation inventory management software emerges as a vital tool, powering mission readiness with unprecedented effectiveness and foresight.
At Greenwood Aerospace, we know a thing or two about efficient inventory management.
As a trusted aerospace solutions company known for delivering exceptional aircraft parts procurement services, Greenwood Aerospace operates at the intersection of technology and expertise. Our proprietary procurement software is a testament to this dedication, providing critical inventory analytics and a database of vetted aircraft parts suppliers.
In this article, we’ll explore the concepts of aviation inventory management, the advantages and challenges within this domain, and spotlight the capabilities of our software.
Let’s start with the fundamentals of aviation inventory management!
The Fundamentals of Aviation Inventory Management
As we prepare to navigate the terrain of aviation inventory management, it is critical to first understand its fundamentals. This involves far more than just stockpiling supplies or maintaining an accurate ledger of assets. Effective inventory management is a multi-faceted endeavor that can streamline operations, mitigate risks, and maximize efficiency.
Key elements of inventory management include:
- Demand Forecasting: Predicting future customer needs based on data and trends.
- Stock Control: Maintaining the right amount of inventory to meet demand without overstocking.
- Safety Stock: Keeping a small surplus to prevent stockouts.
- Inventory Turnover: The number of times inventory is sold and replaced over a period.
- Cycle Counting: Regularly counting parts of your inventory to maintain accuracy.
- Just-In-Time Management: Receiving goods only when needed to reduce costs and waste.
- ABC Analysis: Categorizing inventory based on value and priority.
- Real-time Inventory Management: Using technology to track inventory instantly.
- Centralization and Decentralization: Deciding whether to keep inventory in one central location or multiple places.
While these principles lay the groundwork for effective inventory management, the introduction of aviation inventory management software truly transformed the game. Leveraging advanced technology, these systems automate, simplify, and expedite many of inventory management's traditionally time-consuming and error-prone aspects.
What is Aviation Inventory Software?
Aviation inventory management software, at its core, is a comprehensive tool designed to manage, streamline, and optimize the process of stocking and supplying aviation parts. This specialized software leverages the power of technology to centralize, automate, and simplify various aspects of inventory management, including demand forecasting, inventory control, visibility, and supplier management.
From the humble beginnings of manually maintained logs and ledgers, inventory management in aviation has undergone a significant transformation. As the industry expanded and aircraft technology advanced, so too did the need for more efficient inventory management. Early digital solutions provided basic functionality, allowing for a centralized view of inventory levels and streamlined ordering processes. However, as the industry's requirements grew more complex, so did the solutions, incorporating advanced features such as real-time tracking, predictive analytics, and integration with other operational systems.
One solution for modern demands in procurement service is Greenwood Aerospace's proprietary software—Greenwood Parts Intelligence (GPIQ). Designed specifically for prime contractors supporting special mission aircraft, GPIQ harnesses the power of market intelligence and value enhancement to streamline and optimize the procurement of aircraft parts.
We’ll get into the details of this powerful platform later, but first, let’s discuss the core functions of inventory software and its benefits.
Core Functions of Aviation Inventory Management Software
Aviation inventory management software is a vital tool for aerospace parts distributors. Though features may vary from one software solution to another, the core functions of these systems can be broadly classified into several key categories:
- Inventory Tracking and Control: This allows organizations to keep tabs on the various parts and supplies they have in stock. This can include real-time tracking of inventory levels, location tracking, and automatic reordering when stock levels fall below a certain point.
- Order Management: The software can handle the entire order process, from the initial request through to delivery and invoicing. This includes purchase order creation, approval workflows, and vendor management.
- Maintenance Scheduling: Regular maintenance is vital for aircraft, and this function helps to schedule and track these tasks. It can send reminders when maintenance is due and keep a history of all aircraft sustainment projects.
- Reporting and Analytics: The software can generate various reports and analytics to help with decision-making. This could include reports on inventory turnover, maintenance costs, part usage rates, and more.
- Compliance Management: Aviation is a highly regulated industry, and the software helps ensure compliance with various rules and regulations. This can include tracking of part certifications, expiration dates, and managing recall notifications.
- Forecasting and Demand Planning: The software uses historical data to forecast future demand for different parts and supplies. This helps in planning and ensuring that inventory levels are optimal.
- Integration with Other Systems: This ensures the software can communicate and share data with other systems like accounting, procurement, logistics, etc.
- Document Management: The software helps manage important documents like invoices, purchase orders, certifications, warranties, etc. for easy retrieval and reference.
These platforms have the power to automate the inventory tracking process, provide accurate forecasting for inventory optimization, and streamline supply chain logistics for any aviation program.
Benefits of Implementing Aviation Inventory Software
So, how does this benefit the program? Let’s discuss the top three advantages, which are:
- Improved operational efficiency
- Enhanced financial performance
- Improved customer satisfaction
One of the most significant advantages lies in improved operational efficiency. This software minimizes manual intervention and error probability by streamlining the entire spectrum of inventory processes – from tracking and control to demand forecasting and supplier management. This level of automation liberates staff to focus on more strategic functions of the program. Moreover, the ability to source parts quickly and accurately can significantly reduce downtime and increase the overall operational efficiency of aviation programs.
Enhanced financial performance is another crucial benefit. Efficient inventory management leads to notable cost savings, allowing for accurate demand prediction and avoiding the costly pitfalls of overstocking and understocking. Moreover, the capability to manage suppliers effectively and evaluate their performance ensures the procurement of high-quality parts at the most competitive prices, which translates into further operational cost reduction.
Lastly, the use of software like GPIQ can dramatically increase service levels and customer satisfaction. The efficiency and accuracy offered by these software systems enable aviation programs to uphold their commitments consistently. Reduced downtime and acceleration of parts sourcing result in fewer delays, leading to improved service levels. These enhanced efficiencies invariably lead to heightened customer satisfaction as clients experience less disruption and more reliable service.
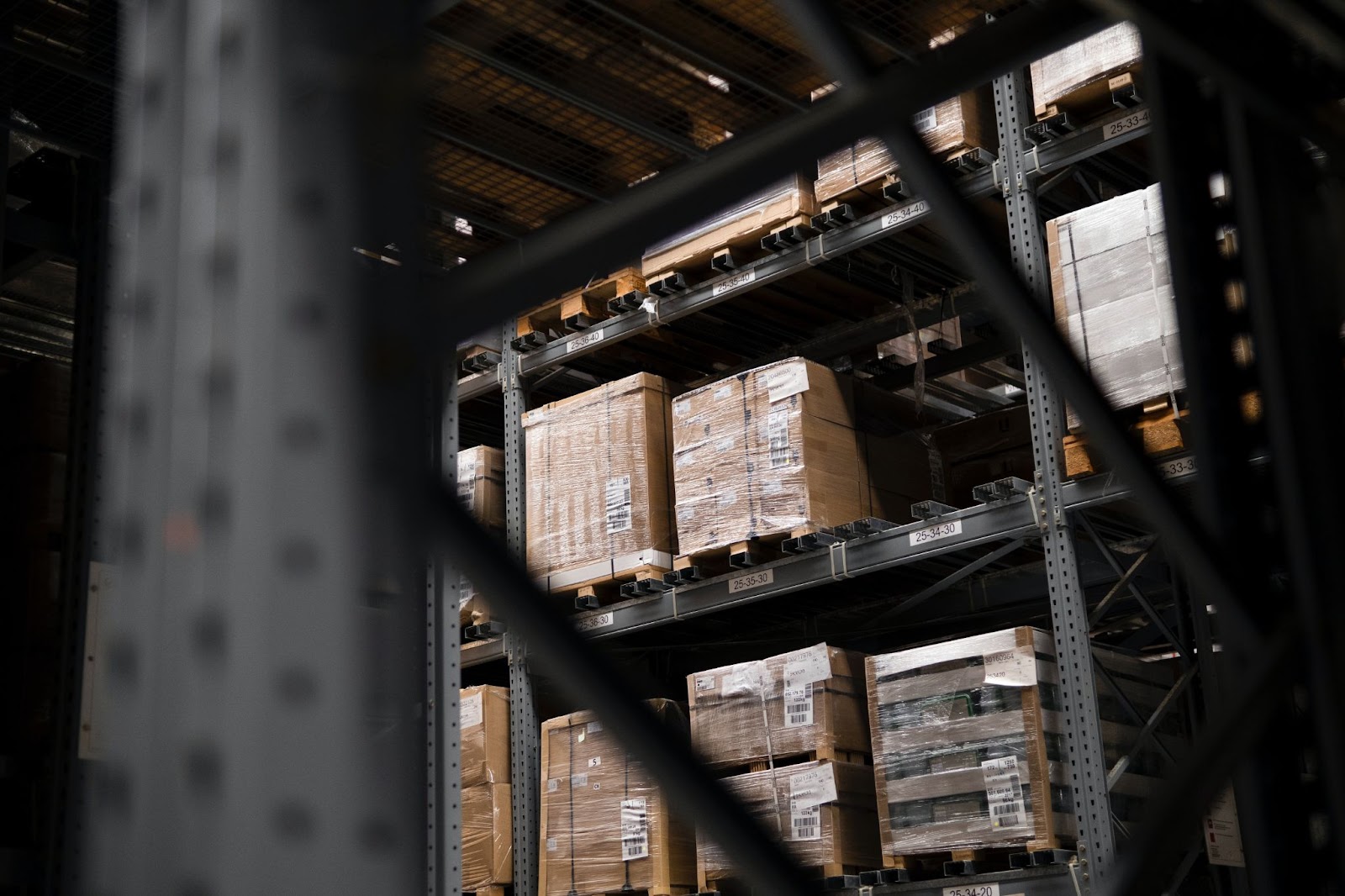
Tackling Challenges in Aviation Inventory Management
Navigating aviation inventory management isn't without its fair share of hurdles. A variety of challenges, ranging from unpredictable demand, supplier reliability, to technological adaptability, frequently arise, each capable of hampering the smooth flow of operations and putting mission readiness at risk.
Take, for instance, the case of an unexpected surge in demand for a particular aircraft part due to an unforeseen technical issue across a fleet of aircraft. This could lead to an abrupt stock depletion, leaving other routine maintenance tasks on hold and aircraft grounded. Such incidents underscore the complex and volatile nature of aviation inventory management, reinforcing the necessity for advanced, adaptable solutions capable of weathering these challenges and leveraging them to enhance operational effectiveness.
As we move forward, we'll explore these challenges in more detail, spotlighting how inventory management software navigates these obstacles, transforming them into opportunities for growth and improvement.
Current Challenges in Inventory Management
In the complex world of aviation inventory management, challenges can emerge as swiftly as an aircraft taking flight. From the intricacies of the supply chain to the unpredictability of demand and the rigors of regulatory compliance, each presents its own unique obstacles.
In this section, we’ll focus on:
- The complexity of the aviation supply chain
- Demand unpredictability
- Regulatory compliance and safety concerns
With many suppliers spread across the globe, the aviation supply chain is inherently complex. Managing relationships with these suppliers, ensuring the timely delivery of quality parts, and mitigating the impact of potential disruptions, all add layers of complexity that can pose significant challenges. Moreover, disruptions in one part of the chain can have a cascading effect, impacting the availability of critical parts and potentially grounding aircraft.
The aviation industry often experiences sudden shifts in demand due to a variety of factors, from unexpected maintenance issues to fleet expansions or retirements. This unpredictability can lead to critical parts being either overstocked, tying up capital, or understocked, risking operational delays.
Apart from its inherent uncertainties, the aviation sector is also subject to stringent regulations enforced by organizations such as the Federal Aviation Administration (FAA) in the U.S. or the European Union Aviation Safety Agency (EASA) in Europe, among others. These bodies mandate uncompromising adherence to standards concerning the quality of aircraft parts, their traceability, and the appropriate disposal of outdated or damaged components. All these are crucial elements in aviation inventory management. Failure to comply with these regulatory requirements can lead to substantial penalties from these agencies, and, more importantly, it can jeopardize the safety of the aircraft and its crew.
In the face of these challenges, inventory management can quickly become daunting. However, with the right tools and strategies in place, these challenges can be transformed into opportunities for optimization and efficiency.
How Aviation Inventory Software Overcomes These Challenges
Addressing the complex challenges in aviation inventory management demands a software solution that is not just robust but also adaptively intelligent. Advanced inventory management software, equipped with powerful features, is designed to navigate these challenges, transforming potential obstacles into opportunities for optimization.
Advanced inventory management software simplifies the multifaceted global aviation supply chain. It allows for the seamless tracking of supplier performance and the negotiation of contracts, ensuring the delivery of quality parts in a timely manner. Real-time data visibility into the supply chain is a crucial feature of these software solutions, enabling operators to anticipate and manage potential disruptions, ensuring a consistent supply chain.
Through the power of real-time data and advanced predictive analytics, these software solutions excel at handling the unpredictable nature of demand in aviation. They leverage historical data and trend analysis to forecast future part demand accurately, aiding in maintaining optimal inventory levels and avoiding the financial and operational pitfalls of overstocking and understocking.
Automation is another critical feature in inventory management software, and it plays a pivotal role in maintaining regulatory compliance and safety. These systems keep track of regulatory-approved parts, monitor their usage, and schedule timely replacements, thereby ensuring adherence to industry standards and minimizing safety risks.
By offering comprehensive reporting and analytics features, these software solutions provide valuable insights that drive informed decision-making. The power to convert vast amounts of data into actionable intelligence equips aviation programs with strategic insights, enhancing their operational efficiency and readiness.
Greenwood Aerospace’s Part Procurement Intelligence Software, GPIQ
Navigating through the myriad challenges of aviation inventory management calls for a trusted and innovative aerospace solutions company. Greenwood Aerospace, with its more than 40-year legacy of excellence and innovation, is precisely that company. Recognized as a trusted provider of aircraft parts procurement for both government and private entities, Greenwood Aerospace has invested in technology to help navigate these inventory management challenges.
We take the capabilities of inventory management software a notch higher, blending state-of-the-art technology with its extensive industry experience to provide comprehensive solutions that address the nuanced needs of the aviation industry.
As we delve deeper into the specifics of Greenwood Aerospace's inventory management system in the following section, we'll see how our company is not just keeping pace with industry challenges, but constantly innovating to stay ahead.
Introducing: Greenwood Parts Intelligence (GPIQ)
One of the cornerstones of Greenwood Aerospace's innovative approach to parts procurement is the proprietary Greenwood Parts Intelligence (GPIQ) software. Designed with the complexity and demanding nature of the aviation industry in mind, GPIQ is more than just a procurement tool.
GPIQ is a dynamic partner that evolves with your changing demands. This system is meticulous, ensuring that suppliers undergo stringent onboarding and qualification tests while providing critical data about their previous performance. This focus on quality control is instrumental in maintaining the high standards of Greenwood Aerospace.
Moreover, GPIQ leverages the power of predictive analytics to manage supplier risk and forecast future demand. This results in a more efficient supply chain, reduced costs, and increased reliability. The strength of GPIQ lies in its role as a strategic ally, managing your procurement expenses for the long term and ensuring you get what you need, when you need it, and at the best possible price.
Complementing this robust software is Greenwood Aerospace's expansive storage facility. Nestled in Ponca City, Oklahoma, the 42,000 sq ft warehouse is centrally located for efficient shipping routes to both coasts. This facility holds large inventories of aviation parts, shop supplies, and ground support equipment, ready to meet your needs swiftly and efficiently.
Features of GPIQ
Greenwood Parts Intelligence (GPIQ) is a potent blend of innovative features, sophisticated technology, and Greenwood Aerospace's deep industry knowledge. Here are the key features of GPIQ that make it a game-changer in the aviation inventory management space:
- Market Intelligence and Value Enhancement: GPIQ leverages robust market intelligence to offer unparalleled insights into the aviation parts market. This allows for more accurate, value-based procurement decisions, enhancing the overall value proposition of procurement operations.
- Stringent Onboarding and Qualifications: GPIQ ensures compliance and quality through rigorous onboarding and supplier qualification processes. This feature provides important information about their previous performance and ensures that all suppliers meet Greenwood Aerospace's high standards.
- Predictive Analytics: GPIQ uses predictive analytics to anticipate future demand and manage supplier risk. This results in accurate demand forecasts, allowing for efficient supply chain operations and minimizing costs.
- Efficiency and Lower Costs: With more accurate demand forecasting and supplier risk management, GPIQ promotes efficient supply chain operations. By reducing the likelihood of overstocking or understocking, GPIQ helps reduce procurement costs, contributing to improved financial performance.
Each feature of GPIQ works synergistically to provide a comprehensive solution that transforms the aviation parts procurement process. From enabling value enhancement to ensuring compliance, from forecasting demand to managing risk, GPIQ addresses every aspect of aviation inventory management, setting new standards for efficiency and reliability.
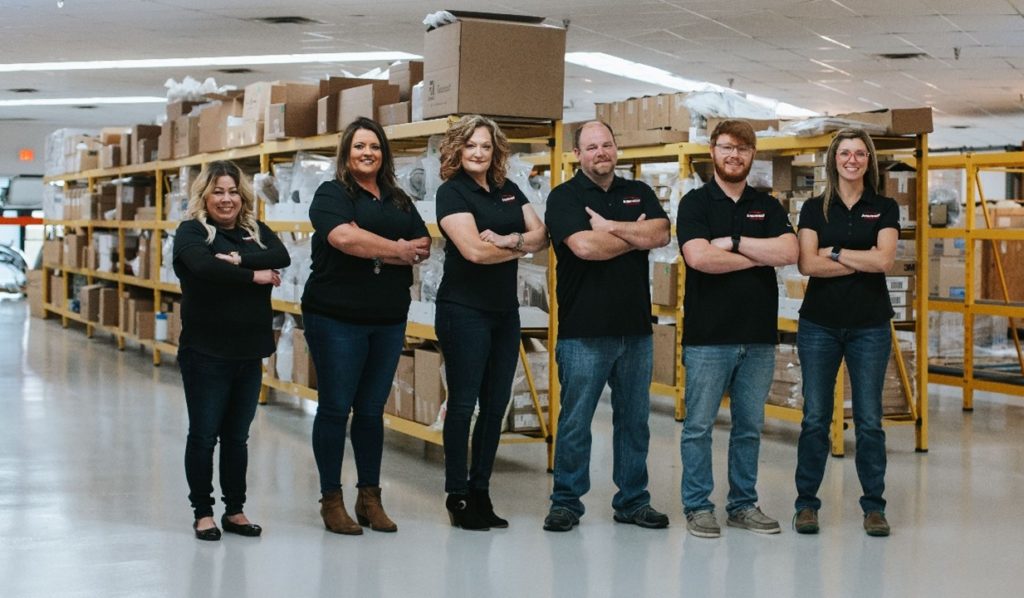
Get Started with Greenwood’s GPIQ
With GPIQ, you're not just investing in a software system—you're choosing a reliable solution that prioritizes your success.
At Greenwood Aerospace, we understand the critical role of efficient inventory management in ensuring your program's success. We're committed to providing state-of-the-art solutions tailored to meet your unique needs.
If you're ready to take your aviation inventory management to the next level, we invite you to contact Greenwood Aerospace today. We'd be delighted to provide you with a quote and show you how GPIQ can transform your procurement operations and enhance your mission readiness. Embrace the future of aviation inventory management with Greenwood Aerospace—we look forward to hearing from you!
Was this article helpful? You may also be interested in: