Hot Section Inspections Revisited - King Air
One of the questions that comes up a lot is about the hot section inspections on PT6A engines that are used in the King Air series of aircraft. These are the most common turboprop engines in the world, being used on the most popular twin-engine turboprop in the world. But even the most popular machines on the planet must have routine service and maintenance because they will end up in the boneyard prematurely without preventative maintenance (PM).
Hot section inspections (HSIs) are a critical inspection cycle to check several crucial parts and areas, including:
- The combustion chamber
- Turbine blades
- Turbine wheel
- Fuel nozzles
- Compressor turbine disk
- Combustion chamber liner
- And compressor blades
There is more than just this in a hot-section inspection, but there are some of the main areas you will be checking. What is a hot section inspection? Let’s find out.
What Is A Hot Section?
Turbine engines are fairly complex, but they are divided simply into two sections: the hot and cold sections.
The hot section of a turbine engine is the part of the engine that is exposed to high temperatures. It includes the combustion chamber, turbine blades, and turbine wheel. The hot section is inspected periodically to ensure that it is in good condition and that it is not damaged.
A turbine engine's cold section is the part that is not exposed to high temperatures. It includes the compressor, the fan, and the gearbox. The cold section is inspected periodically to ensure that it is in good condition and that it is not damaged, but it is not exposed to nearly the same harsh environmental conditions as the hot section.
HSIs are to be performed at the midpoint of the overhaul cycle of a turbine engine; if the TBO is 4,000 hours, the HSI is due at 2,000.
.jpg)
Inspection and Repair of Combustion Chambers
Inspecting and repairing Pratt & Whitney PT6A combustion chambers is a critical part of engine maintenance. The combustion chamber is a complex system that is responsible for igniting the fuel-air mixture and converting it into power. Over time, the combustion chamber can become damaged or worn, leading to engine failure.
The inspection of a combustion chamber typically involves the following steps:
- Visual inspection: The combustion chamber is inspected for any signs of damage, such as cracks, erosion, or corrosion.
- Borescope inspection: A borescope is used to inspect the inside of the combustion chamber for any signs of damage.
- Pressure testing: The combustion chamber is pressure tested to ensure that it is leak-free.
- Dimensional inspection: The combustion chamber is inspected to ensure that it is within the manufacturer's specifications.
The combustion chamber must be repaired or replaced if any damage is found during the inspection. Repairs can be made to the combustion chamber liner, but in some cases, the entire chamber may need replacing.
Turbine Nozzle Inlet Guide Vane Inspection
Inlet guide vanes are a critical component in all turbine engines, whether they are jet engines or turboprops. The IGVs, as they are known, are at the front end of the compressor, and the guide vanes ensure that the expanding gasses arrive at the turbine blades at the proper angle and with the least energy loss. The power turbine portion, which in turn powers the prop shaft through a two-stage planetary reduction gearbox, is propelled forward by the still-expanding gasses.
This makes a lot of sense when you think about what a turbine engine is doing. It operates at all angles of attack, yet the air must impinge the turbine blades at the proper angle. If the air is disturbed, the engine can suffer a compressor surge or a compressor stall, either of which can cause damage or even destroy a turbine engine. You can think of a turbine fan blade as an airfoil, much like a wing. When a wing stalls, there are downstream effects, namely a stall. The compressor stall is no different in this respect. The airfoil is designed for air to flow smoothly over the blades. When airflow separation happens, the airfoil loses its ability to push air in the proper directions at the correct rates; it will surge or stall. IGVs combat this.
Inlet guide vanes are extremely important to maintain and inspect because they are the safeguard against turbulent air entering the compressor. They are simple but effective.
When do you need a PT6 Hot Section Inspection, and what does it involve?
As we said, the HSI takes place halfway through the overhaul cycle. The common overhaul cycles for PT6A engines range from 3,000-4,000 hours, depending on the model. HSIs are then conducted anywhere from 1,500-2,000 hour intervals.
The HSI is now conducted on the aircraft, significantly reducing time and costs. Engine removals should be avoided due to the logistical requirements and added downtime. Thankfully, all of the hot section inspection elements are accessible with the engine on.
Turbine Blades
The turbine blades are the heart and soul of a turbine engine. When turbine blades are damaged even in the slightest, it can impact the efficiency and effectiveness of the engine. This is a great opportunity to inspect, blend, and even replace turbine blades if necessary.
Fuel Nozzles
Fuel nozzles are another highly important area to inspect. The fuel nozzles should produce a “cone” of fuel. Fuel spray patterns are underappreciated; a faulty pattern reduces the burn and engine's efficiency. But it does more than just reduce efficiency: according to Pratt & Whitney, poor fuel nozzle flow significantly reduces hot section life. This makes sense; the fuel is made to flow in a uniform pattern, so if it doesn’t, it can lead to overheating and burning.
The HSI is a great time to conduct preventative maintenance on the fuel nozzles and either clean or fix them as needed. The nozzle hole is only about the size of a pinhole, so it doesn’t take much to clog a nozzle.
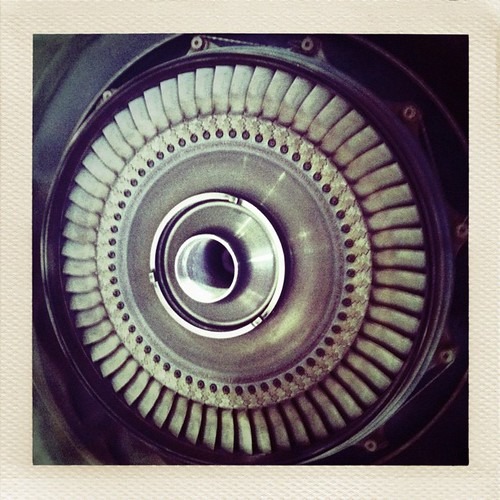
Combustion Chamber
The combustion chamber is sort of the heart and soul of the hot section. It is subject to extreme heat and stress and is prone to cracking. During the HSI, the combustion chamber is inspected to make sure that there are no visible defects.
It’s also a great opportunity to check the other systems and parts in the area, like the igniters, diffuser, case, and liner. This is a good opportunity to replace any parts in the combustion area of the engine and a good opportunity for a parts kit if you know there are things that your maintenance department wants to replace routinely during HSIs.
A Hot Section Inspection (HSI) Is Performed To Ensure the PT6 Engine Is Performing as It Should
As we said, the HSI is an intermediate inspection cycle. It is not an overhaul action, which falls under a different set of requirements. This inspection ensures all systems and components within the hot section are in serviceable condition. Minor repairs and parts replacements are fine; it is a good opportunity to do them. But if significant faults are found, the engine will probably have to be pulled from service (and the aircraft) for deeper diagnosis and repair.
Final Thoughts
In conclusion, a PT6 Hot Section Inspection (HSI) is a critical part of maintaining the safety and performance of your PT6 engine. By following the guidelines outlined in this article, you can help ensure that your engine runs smoothly and efficiently for years to come.
Here are some key points to remember:
- The HSI is an intermediate inspection cycle that should be performed every 1,500-2,000 hours.
- The HSI should be conducted on the aircraft, significantly reducing time and costs.
- The turbine blades, fuel nozzles, and combustion chamber are all critical areas to inspect during the HSI.
- Minor repairs and parts replacements are fine during the HSI, but the engine will probably have to be pulled from service if significant faults are found.
Parts kitting is a great option if there are standard parts that you plan to replace during your HSIs (gaskets, seals, etc.). We suggest you give us a call or start an online quote to build out the kits to your specifications.